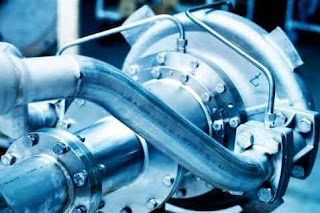 |
Cargo Pump |
The repairs described below are to aid maintenance planning and not a forum for denigrating machinery, companies or personnel
History
The follwing describes a repair to a large twin screw positive
displacement pump. The scrolls where synchronised with a pair of timing
gears fitted to one end. This is one of four installed all of which
had had a history of failure after relatively short run times over a 25
year period (in the region of 6-24 months). Failure normally took the
form of bearing failure, in this case the driven shaft non drive end
bearing had catastrophically failed. The following briefly describes the
repair methods
Investigation
The pump was disassembled with the following damage noted.
The scrolls were in generally good condition with the exception of the
bearing and mechanical seal landing surfaces. These had been repaired
previously using metal spray
Their was general erosion to the casing to about 0.5%of the diameter.
More significant damage was noted to the cutwater beween the two
concentric bores. Due to the advance age of the vessel only the damage
to the cutwater was addressed
Typically the metal spray coaring had detached from the parent metal
under the bearing landings. Thus demonstrating the unsuitablility of
this repair under high impact lading conditions, although it is quite
satisfactory under normal conditions for bearing landings
Normally metal spray repair is satisfactory for mechanical seal landing.
Here is shown a typical poor application of the process. A steel
landing surface should have been available for the seal locating grub
screws otherwise mechanical damage occurs which then allows further
destruction of the coating

It is difficult to show clearly the damage on the drive end bearings but
it was not of the form of pitting and did not appear to be due to the
permenant set damage known as brinelling. A repeat to a lesser extent
was seen on the rolling elements. This was unusual in form and did not
fit the authors understanding of rolling element bearing failure and
caused some confusion. The author offered that very similar damage is
seen in large electrical motors and is caused by electrical discharge
through the bearings. It is noted that this pump is driven by a diesel
engine which also drives an electrical generator via a clutch
arrangement. Similar poor levels of reliability had been seen in the
clutch.
The above and below show a before and after picture of the mechanical
seal. after crack detection two of the four carbons had to be replaced
as well as all rubber seals
Repair
bearing & mechanical seal landings- due to the failure of
previous metal spray repair a different approach was taken. The shaft
was machined and thin steel half segments were welded on and final
machined.It should be noted that the material selected for the shell has
to be galvanically and thermally compatible with the parent metal. The
possibility of building up the parent metal with weld was discounted due
to the poor weldability of the material .
Wear in the timing gear, key and shaft meant that specially offset keys
had to be fabricated to ensure the scrolls were properly centralised.
The pump was preassembled with steel fars taking the place of the main
body. This alowed the scrollsto be accurately centralised using shims
behind the bearings.
With regard to the bearing failures the author informed of the existance
of ceramic coated bearings and the use of shaft earthing rings
No comments:
Post a Comment